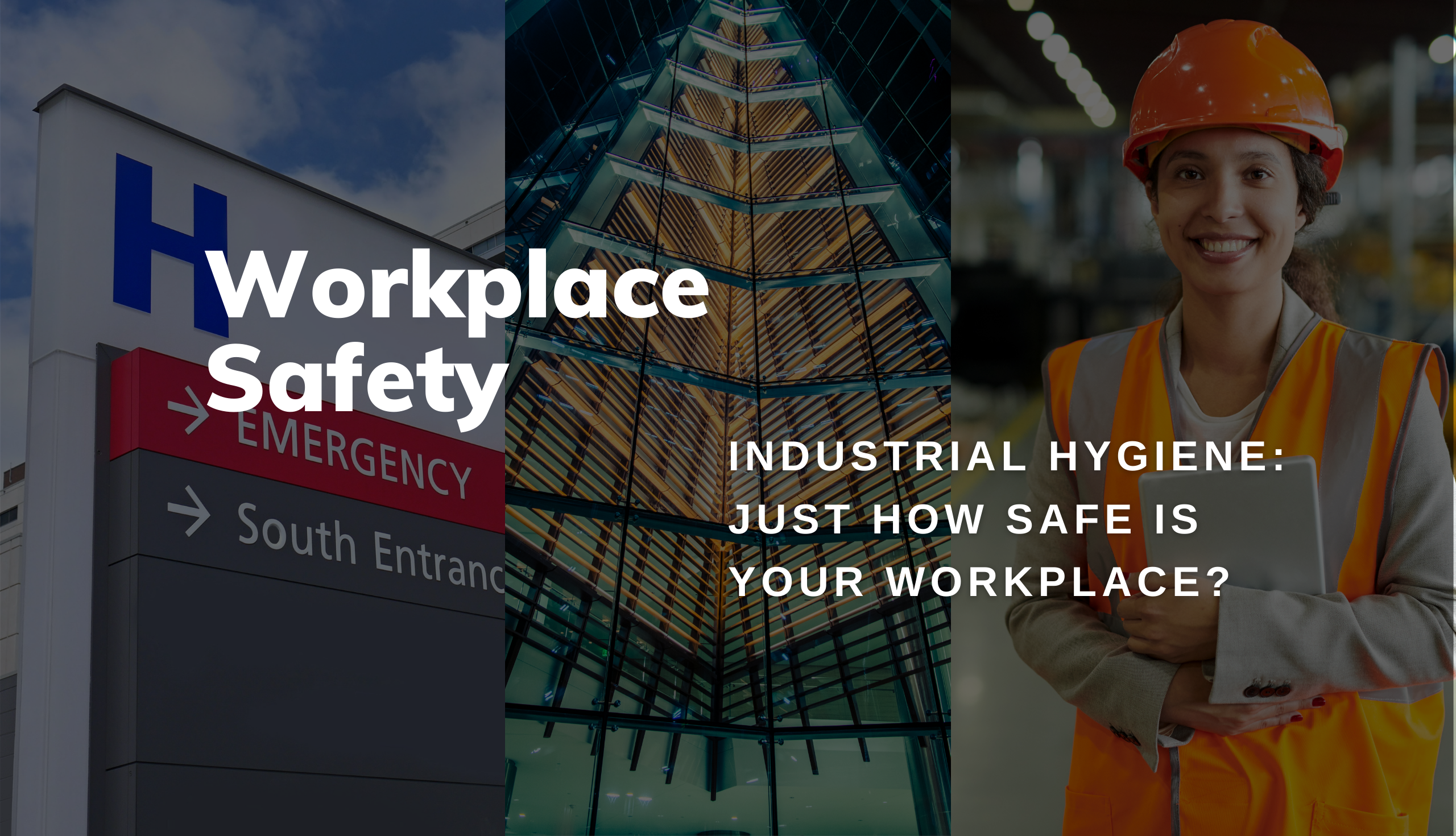
Some estimates suggest that the average person works 90,000 hours over a lifetime. With all this time spent on the job, we would like to assume that our workplaces are safe and healthy environments. Unfortunately, this is not always the case. In many cases, unsafe workplaces or workplace practices can expose occupants and employees to health hazards and risks. This begs the question: Who ensures workplaces remain safe environments for work to occur? The answer: Industrial Hygienists!
What is Industrial Hygiene?
The American Board of Industrial Hygienists defines Industrial Hygiene as the “science of protecting and enhancing the health and safety of people at work and in their communities”. Industrial Hygienists work to evaluate and recognize industrial hazards and develop responses to address workplace hazards so workplaces remain safe.
Workplace Safety Concerns
There are numerous potential hazards that can affect employees’ well-being in the workplace. Such factors can be chemical, physical, biological or ergonomic. Here are a few examples of common workplace concerns that can be addressed by a Certified Industrial Hygienist:
Silica, a chemical agent, is a common mineral found in the earth’s crust. Crystalline silica, also known as quartz, cristobalite, and tridymite, is present in rock, granite, soil, sand, concrete, and many other materials. Common construction activities such as demolition, drilling, and saw cutting these materials create large amounts of silica-containing dust. The smaller the size of the dust particles, the greater the risk of inhaling them. Ultimately, exposure to these particles can result in significant lung damage or silicosis.
Noise, a physical agent, is one of the most common job-related health hazards and is generated from many industrial and commercial processes. Exposure to high levels of noise can cause hearing loss, stress, raised blood pressure as well as various other physiological and psychological health effects. These effects can be temporary or permanent. Overall, the longer the duration of exposure, the more severe the damage will be.
Legionella, a biological agent, is a bacterium that is typically found in freshwater sources, such as lakes and streams. It can grow and multiply in the water systems of homes, hospitals, hotels, and other working environments. People become infected with Legionella by breathing in small water droplets from a contaminated source. This can cause a severe form of pneumonia known as Legionnaires’ disease. This condition results in lung inflammation and can potentially be fatal to people with preexisting health conditions. According to the CDC, there were nearly 10,000 reported cases of Legionnaires’ disease in 2018 (the most recently available data).
Other common workplace concerns are indoor air quality issues, such as lead, asbestos, pesticides, radon gas exposure, ergonomic concerns, and poor ventilation system design. It is vital for employers to understand all potential safety and health hazards in their workspaces so that they may be effectively eliminated or managed.
The Industrial Hygiene Process
Certified Industrial Hygienists use environmental monitoring and analytical methods to detect the extent of worker exposure and employ engineering controls, work practice control, or other methods to control potential health hazards. The role of the Industrial Hygienist is to assess the potential hazard through the following process:
- Anticipate: Sense the presence or potential of hazards without actually observing them
- Recognize: Identify a hazard when it is observed
- Evaluate: Determine what type of harm a hazard is causing and how severe the harm is
- Communicate: Inform others in the workplace or community about the hazard
- Control: Put measures in place to eliminate or minimize the potential of the hazard to create harm, such as injury or illness
Our Services
Do you have additional questions about industrial hygiene or environmental hazards in your workplace? Here at A-Tech, you can speak with one of our in-house Certified Industrial Hygienists regarding any industrial hygiene concern. Our services include:
- Noise Monitoring
- Legionella Testing
- Silica and other Chemical Agents Air Monitoring
- Waste Anesthetic Gas Testing
- Ventilation Testing
- USP 797 Testing
- Office and Industrial Ergonomic Evaluations
- Radon Testing
- Indoor Air Quality Assessments
Every company should make the safety and health of their employees their number one priority. Contact us now to schedule an appointment for these services or any other workplace health and safety concerns and to learn more about our business!
References:
https://www.bls.gov/charts/american-time-use/emp-by-ftpt-job-edu-h.htm